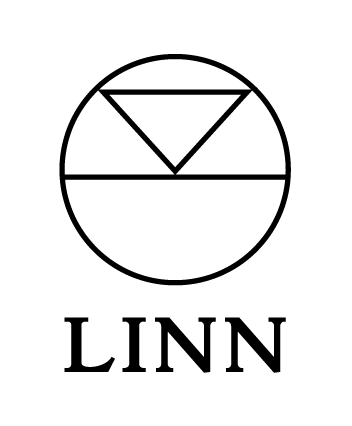
High-End Audio and Heating of Electronic Components in Speaker Systems
Linn Products Ltd. designs and manufactures high-end audio systems, with product lines including pre-configured or customized turntables, network music players, speakers, and power amplifiers. These systems demand high fidelity from the softest whispers to the biggest booming bass, placing extremely high tolerances on the electronic components. The heating of these electronic components during high-power operation can result in degraded performance or even physical damage if critical temperature thresholds are exceeded. Implementing electronic cooling schemes to prevent thermal failure is critical for ensuring long-term performance and reliability.
Thermal Design of Passive Cooling Systems
Thermal management is a critical engineering factor in a wide range of electronic applications. The power dissipated by electrical components can in many cases cause increases in temperature that damage the semiconductor chips or even start fires. The enormous costs and carbon footprint of running water cooling systems to keep server farms running is one famous example. Even for smaller individual systems, such as PCs, gaming consoles, telecommunications equipment, or medical equipment, the worldwide costs of forced cooling add up.
Where possible, it can be advantageous to implement a passive cooling system relying on natural convection; this eliminates the weight and volume that would be taken by a fan, reduces design complexity and cuts electrical consumption costs.
Xi and Linn worked together to model heat transfer of a passive heat exchanger for an upcoming speaker amplifier design consisting of an aluminum “chimney”, to which a power supply and printed circuit boards (PCBs) were mounted. The power supply and PCBs dissipate a significant amount of heat (up to 90 W!) which can cause temperatures that put the control circuitry at risk. Long fins are incorporated along the interior of the heat exchanger to provide greater contact area with the air while maintaining its compact form.
The heat dissipated by the electronics spreads rapidly by conduction through the aluminum chimney and fins, heating the neighbouring air. The air expands with increasing temperature, becoming less dense and rising due to buoyancy forces, resulting in steady natural convection. The hot air continuously exits the top of the chimney and is replaced by cool air at the bottom. When correctly designed, this setup can remove enough heat to keep the power electronics at safe temperatures.
Natural convection, however, is an extremely complex physical process – it is highly nonlinear with respect to power dissipation levels, temperature, fluid density, and flow velocities. For example, if there are too few fins or they don’t have the right shape, there may not be enough surface area for sufficient heat exchange. However, adding too many fins or packing them too densely may constrict flow paths for the air, resulting in insufficient convection. Along with size, weight, and cost constraints, there are always engineering trade-offs; using finite element modelling can help the engineer assess these factors and accelerate the product design process.
How Xi Helped: Thermal Modelling of Passive Cooling Designs for Power Electronics
Xi developed a finite element model of the passive amplifier cooling system, working with Linn’s design and measurement teams, using COMSOL Multiphysics. Thermal physics and computational fluid dynamics (CFD) were directly coupled and solved simultaneously, which is commonly referred to as conjugate heat transfer modelling. The density of the air depends on the temperature, but the temperature depends on the flow rate of the air carrying heat away, but the flow rate depends on variations in its density. This is a complex process, and the governing equations can be highly non-linear.
The printed circuit boards included patches representing the control circuitry which were defined as volumetric power sources. These dissipated power across the boards and heat exchanger by conduction. Because the aluminium material of the heat exchanger has a large thermal conductivity, it was able to spread the heat widely across the structure, allowing more heat to be effectively removed from the large fin surface areas by convection into the air.
A Reynolds Averaged Navier Stokes (RANS) formulation was used to compute the turbulent airflow. A RANS formulation is an efficient way to model turbulent flows because it incorporates turbulent viscosity kinetic energy terms in the flow field which, represent the churn without having to explicitly model individual vortices – such as in a Large Eddy Simulation (LES). This saves on computational time and effort.
Client Benefits
- Computational Fluid Dynamics modelling to understand the effects of design choices on passive cooling performance
- Reduce the time and expenses associated with building and testing large numbers of physical prototypes.
- Accelerate the engineering design process.
- Training on the use of COMSOL Multiphysics for further in-house development.
Collaboration Story
Learn more about this project and the collaboration between Linn and Xi Engineering Consultants in our video: